Applying 5S - Foundation of Quality Management
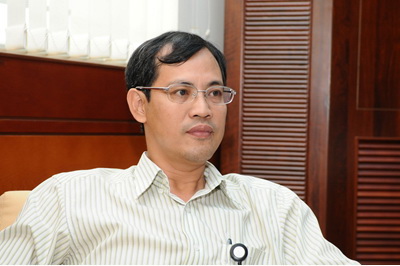
After 5 years of 5S practical application deployment, Petrolimex Saigon Co., Ltd. (Petrolimex Saigon) created remarkable differences in its own culture, strengthened the brand’s reputation, built trust in customers, developed sustainable business. To have a better understanding, Vietnam Trade and Industry Review had the interview with Mr. Dao Van Hung – Quality Department Manager of Petrolimex Saigon – who has passionately done many researchs about 5S thus applied it deeply and perseveringly.
Q: What is 5S, Sir ?
Mr. Dao Van Hung |
A: 5S is a quality and productivity improvement tool originally from Japan. The 5S stand for 5 Japanese’s letters, meaning: (S1) Sort, (S2) Straighten, (S3) Shine, (S4) Standardize and (S5) Sustain.
Sort is sorting out and separate that which is needed and not needed in the area. After that, straighten is arranging all necessary items in regular basic for easily using. Shine is always clean the workplace completely. Standardize is maintaining the first three of the 5S per day, at all times, everywhere. Sustain is the target of all 5S, improving everyday to get the most convenience and effectiveness for working.
Q: Could you tell us whether petroleum business companies necessarily need to apply 5S?
A: The 5S Practice Model is a basis foundation to maintain and improve the management systems follows the worldwide advanced standards. 5S is being applied by Vietnam business organizations and companies in general, petroleum business companies in particular.
Employees work in a shiny cleaning environment, well-equipped, logically ordered have higher working spirit and feel more relaxing; therefore productivity will get higher which is a necessary condition to get the goal of “ Safety – Effectiveness – Satisfying customer needs”.
Q: What are the barriers and difficulties in deploying 5S at Petrolimex Saigon ?
A: Firstly, raising the awareness of staffs and employees about 5S in order to help them understand how many benefits of 5S bring along, therefore creating themselves the professional working habits and attitude. Normally, employees will face many difficulties of changing the old working habits while approaching a new management method, which they need time to improve and adapt. So that, propaganda is needed to be determinatively researched and applied in many cases.
Secondly, the nature of 5S method is visual management. So, establishing visual standards for employees to understand, implement and comply is a great challenge that Petrolimex Saigon has to face with, specially in early stages, when the infrastructure was built up in difference periods of time which is unable to be synchronous. To unite all of the elements of infrastructure, the company need time and rolling implementation performs step by step so that Company can persistently reach the goal, drastically get the targets with flexible methods.
Thirdly, it is strongly commitment of top leadership, and specially shining examples of managers at all levels - important elements to pursue sucessfully 5S program at departments, divisons.
Like Petrolimex Saigon, other business companies and organizations will also face all of those difficuties above at the begin when they apply 5S.
Benefits of 5S brings to companies:
|
A: From the beginning untill now, after 5 years, the 5S practice model has extensively been deployed in all 100% whole company, hetping employees approach systematically to reorganize at the workplace; following established principles and standards; maintaining convenience, quickly, accuracy and effectiveness at the workplace within the company. It can be said that applying 5S have achieved encouraging results.
After 15 years of applying ISO, Petrolimex Saigon has achieved the general Integrated Management Systems for Quality – Safety – Health – Environment QSHE) follow ISO 9001:2008, ISO 14001:2004, OHSAS 18001:2007 and ISO 17025:2005 (the competence of testing laboratories). To position in this management system structure, 5S is the foundation - strongly improvement tool in all activities of the whole company. Maintaining the effectively and efficiently continuous management system of the company currently is a result of 5S improvement tool contribution.
It might be said that the effectiveness of 5S model application brought huge efficiency and extremely significant for the company whose core is to improve productivity, quality and efficiency; improving management system frequently; workplace has become clean, orderly and scientific; employees comply with the work discipline more; supporting conditions are always ready for working; saving time for moving, seeking and specially reducing the hidden costs; work environment has become more safety, performing environmental protection; contributing to enhance the trademark’s prestige, becoming a place to put the belief of customers.
In short, within 5 years, 5S visual management method brought all of the achievements above to the Company.
Q: In all of the achievements that 5S brought to the Company, what are the benefitsthat employees have?
A: “5S - simple, practical and easy to understand” which help all staffs and employees of Petrolimex Saigon to achieve a better awareness, better working habits, more professional attitudes. Logical and professional working skills are great fortune, belonging of employee on the way of contributing and being promoted in career and even in their own daily life.
Currently, everyone organizes work more scientific, orders workplace neatly, better in hygiene and safety, specially the awareness in compliance with management procedures, processes, regulations and standards of the company is improving everyday. Employees work their job in a safe, convenient, united and friendly environment - 5S’s achievement - which is created by collective employees themselves.
Q: What is the improvement of Petrolimex Saigon quality management in general and 5S in particular orientation in near furture, Sir ?
A: At the end of this November, Petrolimex Saigon will organize a conference to summarize the quality work period 2010 – 2015, therefore setting the goals, strategies, solutions and development plans of quality management for the next 5 years - period 2016-2015.
According to those, the company will continue to maintain the integrated management system following standards currently applied; as the same time, expanding the application of specific technical management standards to ensure the depth and synchronization; All are integrated into a general management system to complete “Petrolimex Saigon House of Quality” in order to promote the highest efficiency.
The company will transfer from Total Quality Control (TQC) into Total Quality Management (TQM), completely changing from traditional, experiential, bureaucratic business executive management into scientific, efficient, customer-oriented management follows the philosophy of TQM.
Continuously applying quality improvement tools (5S, Kaizen, Statistical Process Control, Internal Audit, Preventation & Correction, Management Review); among all of those above, 5S is the core and the most basic element. We will have to continuously complete and improve 5S standards therefore getting the quality requirements; besides we frequently train, inspect, supervise and apply the form of rewards, encouragements, even sanctions to promote 5S process faster to go inside the orbit of expectation.
TQM is a customer-oriented method by:
The “Total” word in TQM means covering the whole company and comprehensively controling all elements inside a management system, including 4M +1E: - Men - Method - Material - Machine Environtment |